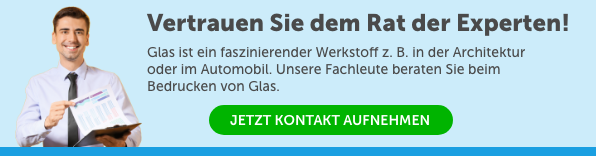
Für die Herstellung von Kalk-Natron-Glas, das ca. 90 % der produzierten Glasmenge ausmacht, werden folgende Rohstoffe eingesetzt:
Altglas oder Eigenscherben aus dem Produktionsbruch werden ebenfalls dem Gemenge wiederaufgegeben – Altglas aus dem Glasrecycling geht vor allem in die Behälterglasindustrie, wo ihr Anteil bis über 90 % betragen kann, und in die Herstellung von Glaswolle, wo ihr Anteil bis zu 80 % beträgt. Dies spart Rohstoff und Energie, da Scherben leichter schmelzen als das Gemenge. Probleme beim Altglasrecycling sind eine schlechte Farbtrennung, Fremdbestandteile wie Metalle, Keramik oder Spezialgläser. Die Fremdstoffe verursachen Glasfehler durch nicht vollständiges Aufschmelzen und Schäden in der Glasschmelzwanne, da sich Metalle in den feuerfesten Boden einfressen. Für Spezialgläser kommen auch Mennige, Borax, Bariumcarbonat und seltene Erden zum Einsatz.
Die Menge des zugeführten Gemenges muss der der Glasentnahme entsprechen. Das Gemenge wird der Schmelzwanne mit einer Einlegemaschine aufgegeben. Bei Temperaturen von ca. 1.480 °C schmelzen die verschiedenen Bestandteile langsam. Die Bewegung der Konvektion im Glasbad erzeugt Homogenität. Diese kann durch ein Bubbling, der Eindüsung von Luft oder Gasen in die Schmelze, unterstützt werden.
Im Läuterbereich, der dem Schmelzbereich unmittelbar folgt und häufig auch durch einen Wall in der Schmelze von diesem getrennt ist, werden in der Schmelze verbliebene Blasen ausgetrieben. Durch die hohe Zähigkeit der Schmelze geschieht dieses nur sehr allmählich, und es sind ebenso hohe Temperaturen erforderlich wie im Schmelzbereich. Da die Läuterung bestimmend für die Glasqualität ist, gibt es vielfältige unterstützende Maßnahmen.
Dem Läuterbereich schließt sich die baulich klar getrennte Arbeitswanne an. Da für die Formgebung niedrigere Temperaturen als zur Schmelze und Läuterung nötig sind, muss das Glas vorher abstehen. Daher spricht man auch von Abstehwanne. Der Kanal, der Schmelzwanne und Arbeitswanne verbindet, heißt Durchfluss und arbeitet nach dem Siphonprinzip.
Bei Flachglaswannen sind Schmelz- und Arbeitswanne nur durch eine Einschnürung getrennt, da ein Durchfluss eine optische Unruhe im Fertigprodukt entstehen ließe.
Von der Arbeitswanne fließt das Glas weiter zum Punkt der Entnahme. Bei der Produktion von Hohlglas sind dieses die Speiser oder Feeder. Hier werden Tropfen in darunter stehende Glasmaschinen geleitet. Bei Flachglas fließt das Glas über die Lippe in das Floatbad.
Je nach Produkt wird Glas unterschiedlich geformt. Die Formung erfolgt durch Pressen, Blasen, Düsen, Spinnen, Walzen oder Ziehen:
Entspannungskühlen
In jedem Glasgegenstand entstehen bei der Formgebung mechanische Spannungen als Folge von Dehnungsunterschieden im Material. Diese Spannungen lassen sich mit optischen Spannungsprüfern messen (Spannungsdoppelbrechung). Die Spannungsanfälligkeit hängt vom Ausdehnungskoeffizienten des jeweiligen Glases ab und muss thermisch ausgeglichen werden. Für jedes Glas lässt sich zwischen der oberen Kühltemperatur (Viskosität von 1013 dPa·s) und einer unteren Kühltemperatur (1014,5 dPa·s), in der Regel zwischen 590 °C und 450 °C, ein Kühlbereich festlegen. Die Spannungen verringert man durch ‚Tempern‘, also durch definiertes langsames Abkühlen im Kühlbereich.
Die Zeit, in der ein Glasgegenstand den Kühlbereich durchlaufen kann, hängt maßgeblich von der je nach Glasart zu überbrückenden Temperatur und der Stärke (Dicke) des Gegenstands ab. Im Hohlglasbereich sind dies zwischen 30 min und 100 min, bei großen optischen Linsen mit 1 m Durchmesser und mehr kann eine langsame Abkühlung von einem Jahr notwendig sein, um sichtbare Spannungen und somit Bildverzeichnungen der Linse zu vermeiden.
Es gibt zwei Arten kontrollierter Temperatursenkung:
Kühlöfen eignen sich nur für Sonderfertigungen und Kleinstchargen, da nach jeder Entnahme der Werkstücke der Ofen wieder auf Temperatur gebracht werden muss. Industriell werden Kühlbahnen genutzt. Hier wird die Produktion auf Stahlmatten (Hohlglas) bzw. Rollen (Flachglas) langsam durch abgestuft geheizte Ofensegmente transportiert.
1. Das flüssige Glas fließt aus der Schmelzwanne in den Feeder. Am Kopf des Feeders formt die Speisermaschine einen länglichen Glastropfen.
2. Der Glastropfen wird über eine Rinne durch den aufgeschwenkten Trichtermechanismus in die Vorform einer Produktionsstation geleitet. Die spätere Öffnung (Mündung) zeigt nach unten (Abbildung 1).
3. Der Vorformboden setzt auf dem Trichter auf und schließt die Form. Von oben wird Druckluft eingeblasen, damit die Glasmasse die unten sitzende Mündungsform ganz ausfüllt (Festblasen, Abbildung 2). Der so genannte Pegel ragt in die Mündungsform.
4. Der Vorformboden und anschließend der Trichtermechanismus schwenken zurück und die Vorform wird mit dem Vorformboden oben verschlossen. Der Pegel bewegt sich nach unten, in die entstehende Öffnung wird durch einströmende Druckluft der Glasbehälter zum Külbel vorgeblasen (Abbildung 3).
5. Die Vorform öffnet sich und das vorgeblasene Werkstück (Külbel) wird vom Übergabemechanismus um 180° in die offene Fertigform geschwenkt (Abbildung 4). Das Külbel wird dabei in der Mündungsform gehalten. Bevor sich die Fertigform schließt, verweilt das Külbel kurz in dieser Position (Rückerwärmen, Abbildung 5). Die Mündung befindet sich nun oben.
6. Die Mündungsform öffnet sich. Der Übergabearm schwenkt zurück in die Ausgangsposition, um den nächsten Tropfen in der Vorform aufzunehmen. Währenddessen wird die Fertigform von oben durch den Blaskopf verschlossen, um das Külbel in der Fertigform durch Druckluft zu seiner Endform auszublasen (Abbildung 6).
7. Der Blaskopf schwenkt zurück, die Fertigform öffnet sich und ein Greifer befördert das fertige Werkstück auf eine luftgekühlte Absetzplatte (Abbildung 7).
8. Ein Abstreifer schiebt das fertige Werkstück auf das Maschinenband, das den Artikel in die Kühlbahn befördert.
Beim Press-Blas-Prozess wird das Külbel nicht geblasen, sondern durch einen durch die Mündungsform eingeführten Pegel gepresst. Es fand zuerst bei weithalsigen Behältern (zum Beispiel Konservengläser) Anwendung.
Allerdings bringt das Press-Blasen von enghalsigen Flaschen entscheidende Vorteile: Das Külbel kühlt sich beim Pressen stärker ab, dadurch ergeben sich höhere Produktionszahlen. Da die Glasverteilung im Külbel durch Pressen besser beeinflussbar ist, können zudem dünnwandigere Glasbehälter wie Leichtgewichtsflaschen gefertigt werden. Daher findet das Press-Blasen immer mehr Einzug in die Flaschenproduktion und wird hier als Enghals-Pressen bezeichnet. Der Enghals-Press-Blas-Prozess gilt als die modernste Stufe der Glasverarbeitung.
Im Gegensatz zum Blas-Blas-Prozess wird beim Press-Blasen die Mündung zuletzt ausgeformt. Daher muss das geforderte Tropfengewicht sehr genau eingehalten werden, damit es nicht zu unfertigen Mündungen kommt. Der Maschinenführer wird dabei oftmals durch automatische Messsysteme unterstützt, z. B. Pegelstellungskontrolle oder automatische Regelung des Tropfengewichts.
Das Blas-Blas- und das Press-Blas-Verfahren sind in der Hohlglasproduktion am weitesten verbreitet, durch Umrüstung beherrschen die meisten Produktionsmaschinen beide Verfahren.
Eine IS-Maschine (benannt nach ihren Erfindern Ingle und Smith) ist eine Aneinanderreihung einzelner Produktionseinheiten, die unabhängig voneinander Behälter produzieren. Oberhalb der Maschine am Feederkopf befindet sich eine Speisermaschine, die mit gekühlten Messern einzelne Glastropfen schneidet, welche dann über ein Rinnensystem und den Tropfenverteiler den Produktionssektionen zugeführt werden. In den Stationen werden die Posten in einzelnen Schritten im Blas-Blas- oder im Press-Blas-Verfahren zu fertigen Behältern verarbeitet und über ein Transportband in die Kühlbahn transportiert. Der Antrieb der Maschinen erfolgt pneumatisch oder bei neueren Typen über elektrische Servoantriebe.
Die ersten IS-Maschinen bestanden aus 4 Sektionen. Das Umlenken der Glasposten und Laden der Stationen stellte die Entwickler der IS-Maschine vor große Probleme, so dass zunächst maximal vier Stationen aneinandergereiht werden konnten. Moderne IS-Maschinen produzieren heute bis zu vier Flaschen pro Station auf bis zu 16 Stationen gleichzeitig.
Die IS-Maschine ist die am weitesten verbreitete Maschine in der Hohlglasproduktion. Sie arbeitet immer nach dem Blas-Blas- oder dem Press-Blas-Verfahren. Hersteller von IS-Maschinen sind unter anderem Emhart Glass (Schweden / Schweiz), GPS (Essen, Deutschland – zu Saint Gobain Oberland), Heye International (Obernkirchen, Deutschland – zu Ardagh Glass), Owens-Illinois (USA), Bottero und BDF (beide Italien), Sklostroj Turnov CZ (Turnov, Tschechische Republik).
Rundläufer- oder Karussellmaschinen bestehen, im Bereich der Hohlglasproduktion, aus 7 bis 10 Produktionssektionen, die auf ein Karussell montiert sind. Eine oberhalb der Maschine befindliche Speisermaschine formt einen Glasposten, der in die einzelnen Stationen fällt. Zum Laden der verschiedenen Stationen werden die Formen jeweils um eine Station weiter gedreht. Im Laufe einer 360°-Drehung werden die einzelnen Produktionsschritte ausgeführt. Rundläufer sind zudem nicht nur auf den Blas-Blas- und den Press-Blas-Prozess beschränkt, sondern finden auch beim Pressen und Schleudern (siehe unten) Anwendung. Da bei Rundläufermaschinen eine gewaltige mechanische Masse in Bewegung gehalten wird, ist die Geschwindigkeit des Prozesses begrenzt.
Rundläufer finden vor allem in der Produktion von Weingläsern und anderen hochwertigen Trinkgefäßen im Paste-Mould-Verfahren sowie generell bei der Herstellung von Gefäßen, die keine Massenware (Getränkeflaschen, Konservengläser, Parfumflakons) sind, Verwendung.